Each week, many Americans dutifully separate their plastic waste for recycling, hoping to contribute to a greener future. However, conventional recycling methods have limitations when it comes to handling various plastic materials, including flexible films, multilayer plastics, and colored plastics. As a result, only about 9 percent of plastic waste in the United States is typically recycled into low-value products. In an exciting breakthrough, chemical engineers at the University of Wisconsin–Madison have developed a novel technique that promises to convert low-value plastic waste into high-value products, potentially revolutionizing the recycling industry.
A Sustainable Solution:
Published in the August 11 issue of the journal Science, this innovative method not only offers a pathway to enhance economic incentives for plastic recycling but also opens the door to recycling previously challenging plastic types. Moreover, the researchers estimate that their method could reduce greenhouse gas emissions from conventional industrial chemical production by a remarkable 60 percent.
The heart of this recycling breakthrough lies in two existing chemical processes: pyrolysis and homogenous hydroformylation catalysis.
- Pyrolysis: In this step, plastics are heated to high temperatures in an oxygen-free environment, resulting in pyrolysis oil, a liquid mix of various compounds. This oil contains substantial amounts of olefins, which serve as crucial building blocks for various chemicals and polymers used in the industry.
- Homogenous Hydroformylation Catalysis: Unlike traditional energy-intensive methods for producing olefins, which rely on subjecting petroleum to extreme heat and pressure, this process employs olefins extracted from pyrolysis oil. It converts these olefins into aldehydes, which can be further reduced into valuable industrial alcohols.
The products obtained through this recycling process can be utilized in the production of a wide range of higher-value materials. These include key ingredients for soaps, cleaners, and other useful polymers, making it a highly promising and versatile technology.
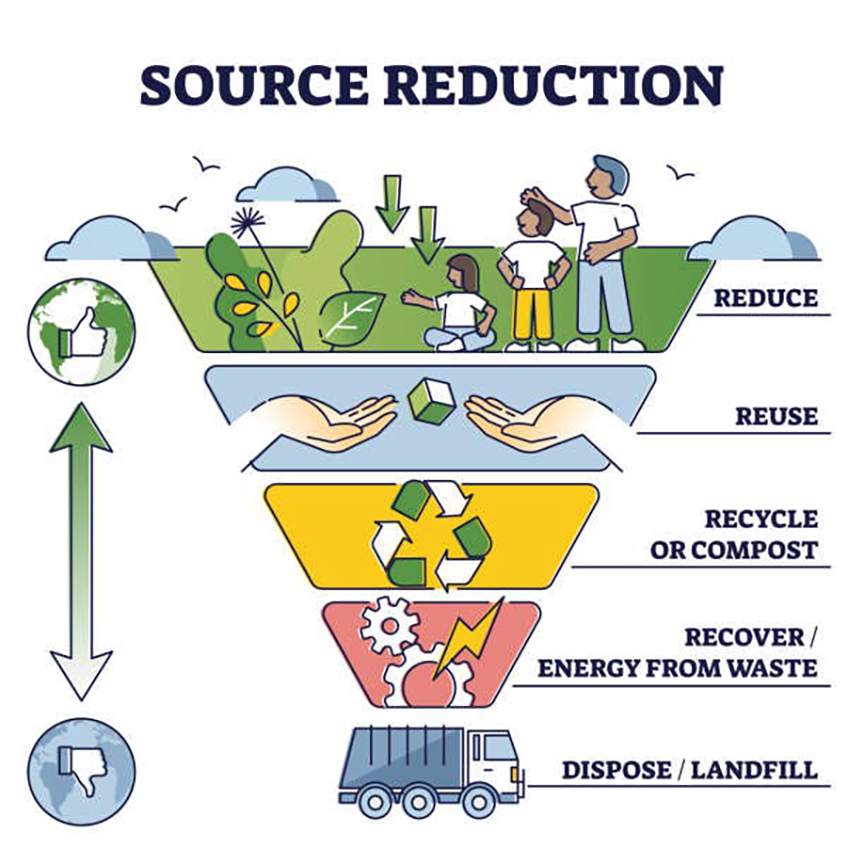
According to George Huber, a professor of chemical and biological engineering who led the research, the recycling industry is poised to embrace this technology. Several large chemical companies have already started constructing facilities to produce pyrolysis oils from waste plastics. However, the challenge has been upgrading these oils into high-value products. The new chemical recycling method provides a sustainable and potentially lucrative solution, as it can yield alcohols worth $1,200 to $6,000 per ton from plastics that are otherwise valued at around $100 per ton. Importantly, the process builds upon existing technologies, making it relatively easy to scale up.
The success of this innovative recycling process is the result of a collaborative effort across various departments at UW–Madison. The involvement of experts in chemistry, modeling, and economics has made it possible to address the complex challenges posed by plastic recycling.
The research team’s next objective is to fine-tune the process and gain a deeper understanding of which combinations of recycled plastics and catalysts produce specific chemical products. The versatility of this technology offers numerous potential product avenues, ultimately challenging and potentially changing the landscape of the plastic recycling industry, turning waste into a valuable resource for the benefit of both the environment and the economy.