In 2021, global construction projects devoured a staggering 30 billion tonnes of cement to produce concrete, each tonne emitting nearly a tonne of carbon dioxide (CO2). While this paints a bleak picture of the environmental impact of the construction industry, there’s a glimmer of hope. Innovative technologies are already available to mitigate the carbon footprint of concrete production.
The world’s attention will turn to Paris, France, next summer for the 2024 Olympics. The organizers are confident that these Games will set a new standard for sustainability. They have pledged to implement numerous energy-conservation initiatives and creative innovations aimed at cutting in half the typical greenhouse gas emissions generated by hosting such a global event. These efforts will span areas like food sourcing, energy generation, and transportation.
One shining example of sustainable innovation can be found in the newly constructed Athletes’ Village, located just over four miles from the heart of Paris. This vibrant neighborhood, comprising the Olympic Village Plaza, a residential area, and an operational zone connected to major road networks, is predominantly built with concrete. However, it’s not just any concrete; it’s ultra-low carbon cement developed by Ireland-based Ecocem in partnership with global construction firm VINCI Construction. Known as Ecocem Ultra, this cement significantly reduces the CO2 footprint of the entire project. It’s a hydraulic binder produced without the high-heat, high-emission combustion process typically associated with cement production.
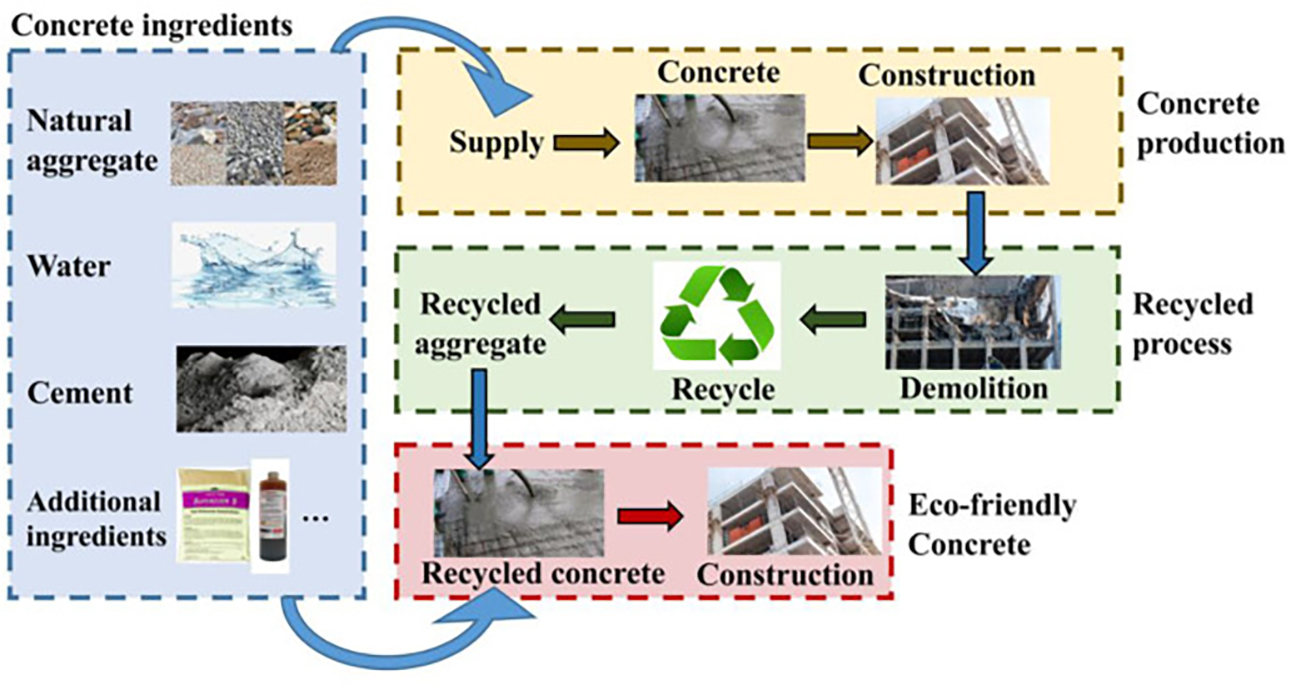
Ecocem is one of several companies that have emerged in recent years to provide much-needed low-carbon cement alternatives. Concrete is the second-most consumed substance globally after water, shaping urban landscapes worldwide. Demand for concrete has nearly tripled over the past two decades, reaching a staggering 30 billion tonnes in 2021, equivalent to three million Eiffel Towers. Alarmingly, cement production accounts for 8 percent of the world’s GHGs, with every tonne of cement manufacturing emitting nearly a tonne of CO2.
The primary culprit behind these emissions is the chemical reaction called calcination, where heating limestone (calcium carbonate) produces lime (calcium oxide), releasing substantial carbon into the atmosphere. The high-temperature kilns used in this process burn significant amounts of coal and petroleum coke, fossil fuels that not only emit CO2 but also other harmful pollutants like sulfur dioxide and nitrogen oxide, contributing to air pollution and adverse health effects. Moreover, mining and quarrying for limestone and clay are linked to deforestation and biodiversity loss.
The good news is that technology exists to reduce the environmental impact of concrete production. While reducing clinker usage is challenging, substituting traditional cement with less harmful alternatives offers promise. Companies like Eco Material Technologies in North America are leading the way by using “supplementary cementitious materials,” primarily recycled fly ash from power plants that would otherwise go to waste. This approach not only reduces emissions and costs but also enhances concrete strength.
Eco Material Technologies continues to refine its production methods, increasing the proportion of carbon-free cement in its products. In the United States, other startups like Watershed Materials and Fortera are developing alternatives, including clay-based cement and CO2-absorbing materials that reduce emissions by over 60 percent while remaining cost-effective.
The adoption of circular business models, such as using digital marketplaces for waste and embracing circular technologies, could yield substantial benefits. According to McKinsey, this transition could deliver an extra €110 billion in net value and prevent two billion tons of CO2 emissions by 2050 for cement companies.
To make low-carbon cement and concrete the norm, policy changes are crucial. The Alliance for Low-Carbon Cement and Concrete (ALCCC), a coalition of European innovators and construction firms, calls upon the European Union to establish ambitious targets for low-carbon, resource-efficient, and circular construction products. This includes revising legislation, standards, and financial tools to reduce the environmental impact of concrete.
Ultimately, the path to sustainable concrete production lies in innovation, collaboration, and the commitment to reshape the construction industry for a greener future.