Spring in Switzerland heralds not just the emergence of snowdrops and crocuses but also the commencement of road construction projects. Repair work, patching, and renovations abound, and while some of the old asphalt from the Swiss road network finds new life through recycling, approximately 750,000 tons still find their way into landfills every year, forming ever-growing black mountains. The consensus among the federal government, cantons (major road owners), and the Swiss populace is clear: these asphalt mountains must be reincorporated into the Swiss road infrastructure. However, given Switzerland’s advanced state of development with minimal new road construction, maximizing the use of recycled asphalt is paramount for sustainability.
Empa researcher Martins Zaumanis emphasizes the importance of understanding the interplay between reclaimed asphalt and new material, adapting production processes, and providing practical guidance and tools to the industry. These objectives served as the foundation for the HighRAP research project, conducted in collaboration with the Federal Roads Office (FEDRO), the Federal Office for the Environment (FOEN), the cantons of Zurich and Graubünden, and various industry partners from 2019 to early 2023.
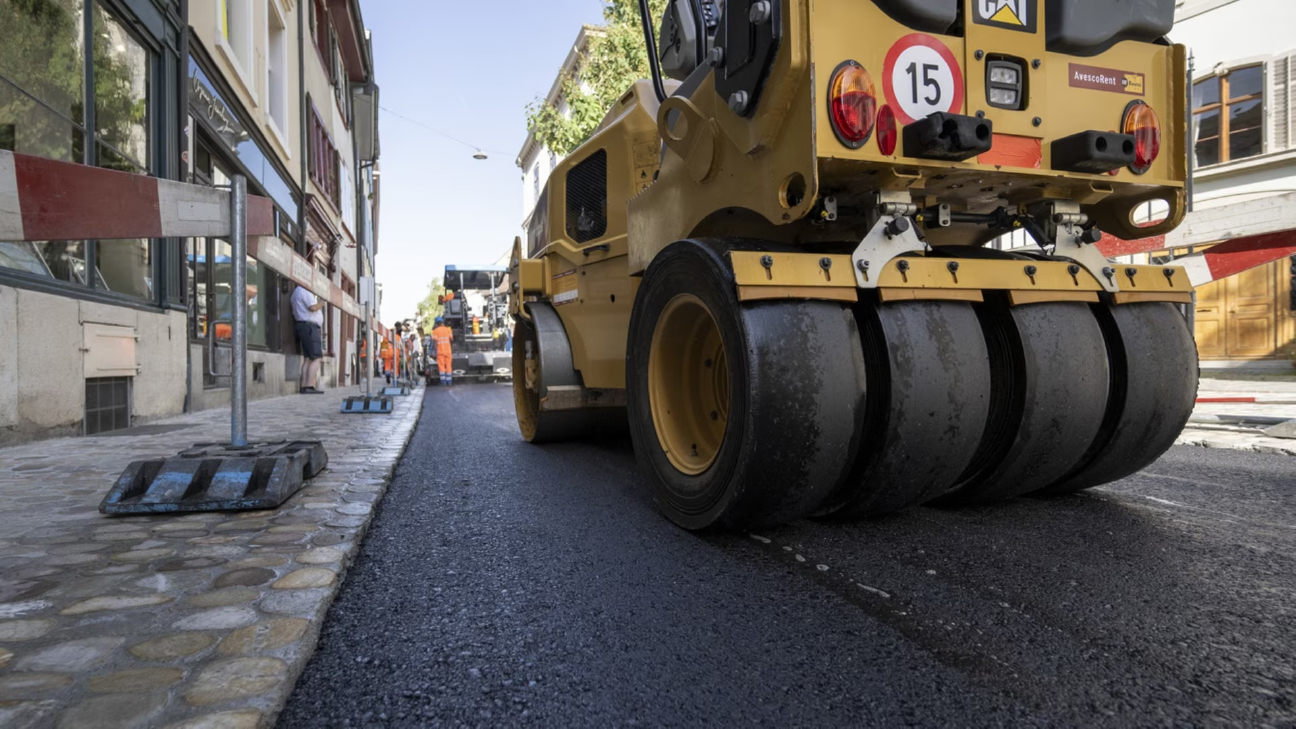
Asphalt comprises an aggregate mixture and the binder bitumen, which is sometimes modified with polymers for heavy-load roads. Historic limitations on using reclaimed asphalt pavement (RAP) for new road construction stem primarily from bitumen aging over time, leading to stiffness and susceptibility to cracking. Additionally, achieving homogeneity with RAP poses challenges as materials from different road layers and of varying ages merge, along with differences in granule sizes. Traditional design methods and standardized quality control tests struggle to adapt to incorporating RAP into production processes.
To increase the RAP content in road construction, innovations are essential, encompassing both the removal and processing of old asphalt. Effective recycling preserves the original aggregate and minimizes dust production. Zaumanis introduces practical criteria and calculation models for characterizing RAP processing, including permissible variability based on future applications. He also presents a pragmatic calculation model for the dosage of “rejuvenators,” substances that soften reclaimed asphalt’s old binder to make it reusable.
The production of asphalt with RAP is more complex due to the multitude of materials and substances involved. Uncertainty about material properties and interactions necessitates performance-based testing methods, examining the material for signs of cracking or plastic deformation.
The ultimate test lies in real-world applications, which instill confidence in asphalt with a high RAP content. As part of the HighRAP project, asphalt with significant RAP content has been laid on two road sections, offering diverse challenges. In Uster, a RAP content of 30% in the wearing course exhibited no loss of performance, while the binder course accommodated between 40% and 50% RAP. At the Lukmanier Pass, exposed to harsh climatic conditions, an asphalt with 85% RAP content in the foundation layer and 70% RAP content in the base and binder layers demonstrated resilience to temperature fluctuations and cracking.
These test sections will be monitored for years to study RAP asphalt’s long-term behavior, with optimism that the black mountains of landfill-bound asphalt may no longer loom large. Political initiatives advocating a landfill ban on reclaimed asphalt and projects like HighRAP are paving the way for a more sustainable approach to asphalt recycling.